Paul's been making some good progress on his sedan. It's sitting channeled 4" and the motor mounts and the front suspension are well underway.
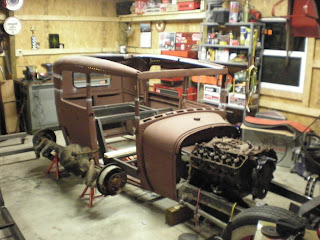 |
Ford 429 and Toploader trans mocked up. |
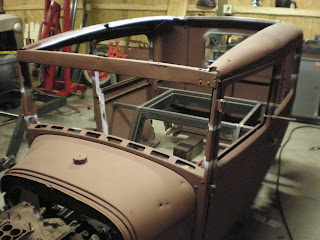 |
Sub-frame DONE! |
|
|
|
|
He called me up to help him give the sedan a haircut. He laid out the 5.75" chop at the pillars with some masking tape and a spray can and we went at it. His weapon of choice was a saws-all with a nice new thin steel blade. I was surprised how quickly we cut through, no rusty pillars here, I mean this thing is solid!
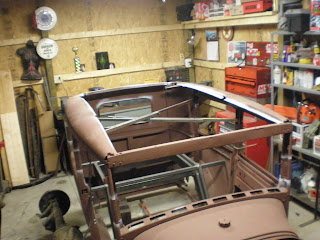 |
X-brace in the roof. |
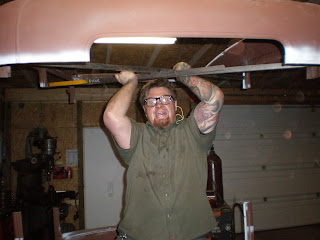 |
Byaaaahhhhh!! |
Paul trimmed up the bottoms of the pillars and we set the top back on. I love those moments when you step back to look at the badassness you've created, this was definitely one of those moments. The almost 6" chop is serious! Combined with a 4" channel, there's not a lot of room left!
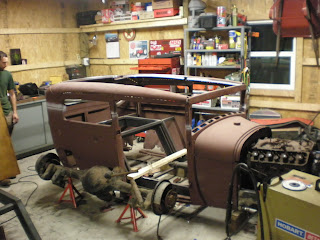 |
Looks bitchin! |